Smart lab power supply for IoT and embedded devices
Smart lab power supply for IoT and embedded devices
When we embarked on the journey to bring Otii solution to the market, we really wanted to offer a comprehensive tool for measuring and optimizing device current consumption. We are happy to see the many different ways our customers are using our products, fully leveraging their multifaceted capabilities. One of the simplest yet highly valuable features is Otii Ace/Otii Arc being a really smart lab power supply. Essential for both hardware and software developers, a lab power supply stands as a fundamental tool in the routine development of IoT and embedded electronics.
Programmable power supply
Despite their sleek appearance, Ace and Arc feature all the essential controls of a typical lab power supply, such as voltage level and current limit control. It is a digitally controlled power source offering control over different settings, including variable voltage, current, power, and mode of operation.
Contrary to standard power supplies with front panel controls, all adjustments and monitoring in Arc and Ace are performed via the Otii UI on your computer supported on Windows, MacOS and Ubuntu.
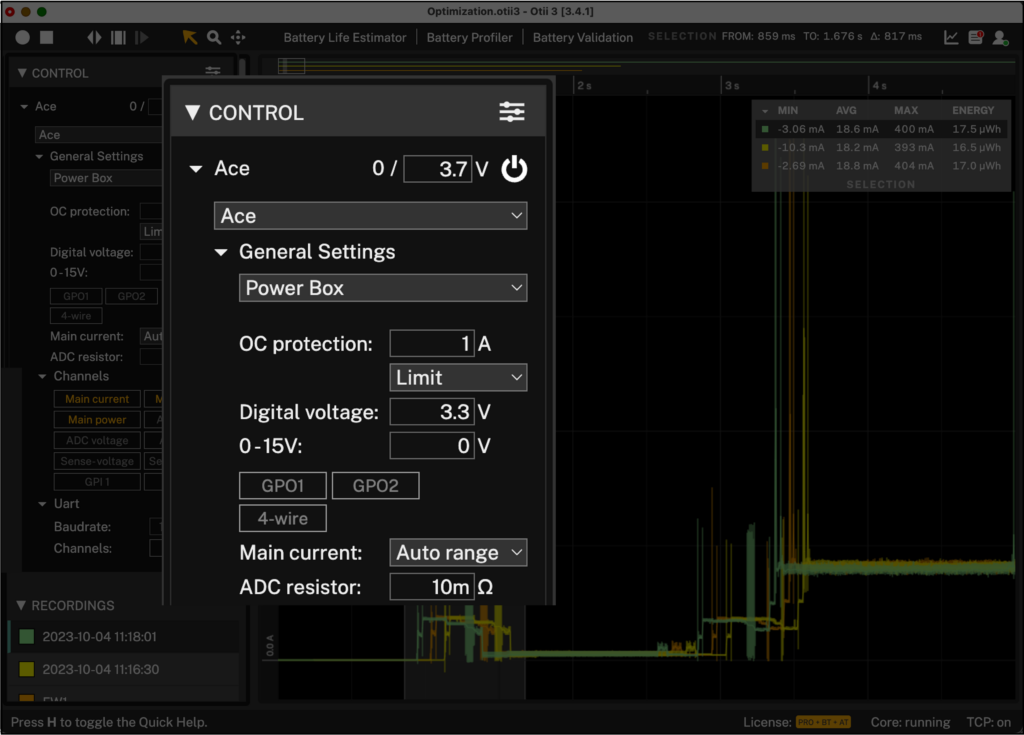
Power and measure simultaneously
Otii is as a combination of a lab power supply, a current probe and an oscilloscope. When testing a new device/module/chipset feature, monitoring the current to verify the circuit’s behavior is a must. This is especially important at the power up of the IoT or embedded device. Different parts of the device power up with different timings. There are delays between different activities and software needs to boot up. Hence, it’s important to distinguish any anomalies in this process. Unexpected current transients that would not have been visible on an ordinary current meter, are easily spotted with Otii Arc/Ace. The high dynamic range (24 bits) of the current measurement makes even small anomalies visible.
Additionally, the logging of current and voltage, and other metrics thanks to the I/O interface, allows the user to understand what draws the current and affects the battery life of the device being developed.
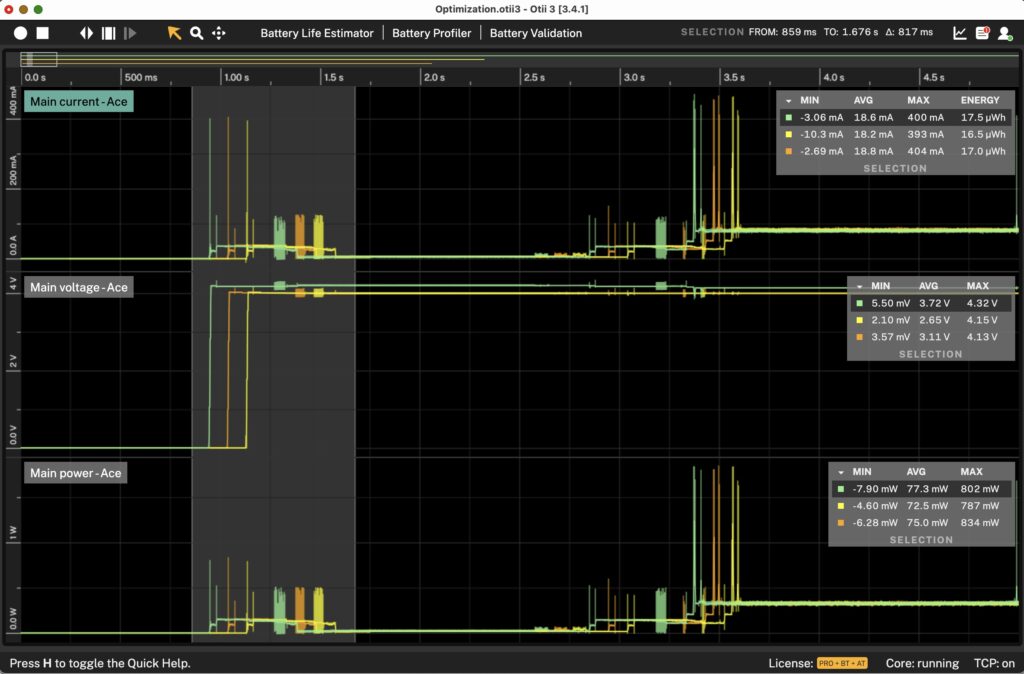
Otii Ace is an isolated power supply
In isolated power supplies, the input side and the output side are electrically separated using transformers or optocouplers. This configuration provides several advantages compared to non-isolated power supplies, but it also comes with a higher cost.
The power supply for Otii Arc and Otii Ace differs not only in their power delivery capabilities but also in whether they are isolated or not.
Otii Arc
The power supply of Otii Arc is not isolated, meaning that the low side of the power supply (main -) is connected to ground potential, which is the same potential as the USB port ground, DC plug ground, and the expansion port ground pins of Otii Arc.
Otii Ace
On the other hand, Otii Ace is an isolated power supply. It is isolated both from the expansion port ground pins and from the USB connector and DC plug ground.
Having an isolated power supply offers several benefits:
1. Ability to connect in series with another power supply
Otii Ace can handle up to a 200V difference between the power supply ground, the expansion port ground, and the USB/DC plug ground.
2. Avoidance of group loops
Ground loops can introduce noise into measurements. By using an isolated power supply, you can minimize the impact of ground loops and improve measurement performance, especially in cases where there is 50 or 60Hz noise.
3. Safety
Although the voltages involved are low in the case of Otii Ac/Ace, having an isolated power supply adds an extra layer of safety.
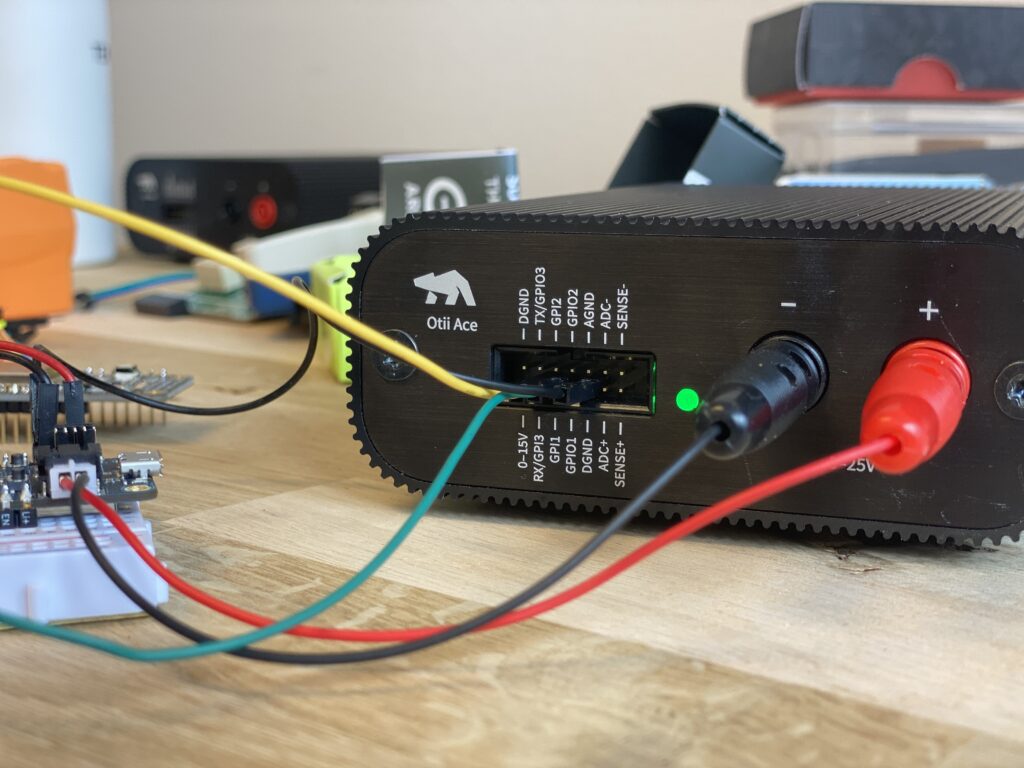
Otii Ace Pro is also an isolated power supply.
When isolated power supply comes in handy
An example that illustrates the need for an isolated power supply is when an IoT system includes a fuel gauge connected to the low side of the battery, which may not be at the same potential as the system ground. If the expansion port ground is connected to the device under test (for UART or GPIO, for example), it could result in a short circuit and incorrect measurements from the fuel gauge in the case of using a non-isolated power supply.
However, with Otii Ace, which is isolated between the main, expansion port, and USB/DC plug, you would need to connect the expansion port digital ground (DGND) to use digital signals (UART and GPIO) and the expansion port analog ground (AGND) to utilize SENSE+, SENSE-, or ADC voltage.
Generating negative voltages is another valuable use case for isolated power supplies. By connecting two isolated power supplies in series and using the midpoint as a ground reference, it is possible to create a power supply that provides both a negative voltage and a positive voltage. This configuration is predominantly employed in applications that deal with audio signals or the development of analog electronics.
When the oscilloscope is not enough
Imagine a scenario in the early development stages of an IoT device, characterized by its miniature PCB and ultra-small components, where a critical issue arises during the power down sequence.
Typically, one would solder small wires to ultra-tiny pads on the PCB, followed by monitoring and capturing the behavior using an oscilloscope.
Usually, it’s not possible to put a probe on the wanted signal when the signal travels from one BGA to another BGA well buried in a multilayer PCB. By monitoring the behaviour of the current with Otii Arc or Ace, it is possible to track down the error. After correction, the correct behaviour is easily verified using the same method. In this instance with our customer, the exercise was used to compare against the original measurements, providing a visual reference for the development team to use in the future.
Summary
A lab power supply is not just a fundamental necessity in the world of IoT and embedded electronics development. For hardware and software developers alike, choosing a programmable and isolated power supply offers unmatched versatility, adapting to a wide range of project needs. Moreover, selecting a supply capable of simultaneously measuring power consumption can be incredibly cost-effective, streamlining processes and reducing the need for multiple tools. The right power supply can significantly enhance your development workflow, making it an investment worth considering for anyone in this dynamic field.
Want to know more?
Do you have any questions on this topic? Contact us to learn more.
Related products
Become a member of our community
Gain access to exclusive resources, educational materials, and expert advice to enhance your knowledge and understanding of powering IoT devices and battery testing.